How to Select and Maintain Thermal Analysis Hardware and Software?
Your choice of thermal analysis technology, technique, and software depends on the nature of your operation and local goals.
For most industrial facilities or solar farms, we find that measuring relative temperatures using qualitative inspection techniques, such as a drone-enabled overview or facility scan, is sufficient for annual inspection purposes. This inspection process identifies most anomalies—cold or hot spots, loose connections, among others — to the degree necessary to inform further detailed investigation and, ultimately, any correction.
The systems used for qualitative inspections are less expensive, easier to use, and require less stringent certifications than hardware and personnel for quantitative inspections.
For qualitative inspections, a thermal imager that shows temperature gradients but does not calculate specific temperatures may be good enough. However, for quantitative thermal reviews, you need a radiometric imager that calculates spot temperatures at each pixel.
Consider the type of inspection, the accuracy required, and how the inspection supports the documentation needed when selecting the appropriate technology.
A hand-held thermometer provides a spot temperature reading but does not provide a thermal image that can be saved and compared visually. A thermal imager provides visual feedback but no specific, measurable temperatures, while radiometers offer accurate measurements and visual feedback.
Tune your selection based on your specific requirements and the effectiveness/cost trade-offs implied.
IR thermographic equipment or systems are measurement systems. For consistency and accuracy, as with all essential measurement systems, we recommend you periodically recalibrate the imager or radiometer to ensure valid results. Do not undertake quantitative thermal analysis or inspection without a properly calibrated system.
Consider the calibration requirements and challenges when selecting your thermography equipment. For example, if the equipment must be sent to the supplier for calibration each year, you incur additional costs and lower utilization of your equipment. Factor the calibration costs into the total cost equation.
The high-accuracy IR thermal analysis systems’ up-front purchase price is relatively high, but so are the costs of misdiagnosis in a mission-critical environment.
Regardless of the solution selected, if you manage the process with your internal resources, the system used is only as good as the training provided to your operators. Do not skimp on training.
Given the various variables at play, from the training required for accuracy to maintenance costs, we recommend a total cost approach to understand the difference between various technologies and strategies.
When selecting an approach (in-house versus contract) or a system, consider the value of accurately determining a quantitative temperature, reducing the diagnostic and repair cycle time, and the financial risk of unplanned outages when you miss a faulty component.
Take a life-cycle total-cost approach to weighing the benefits and costs of each solution. A system that is pricier up-front may be the most cost-effective over time.
Cheaper solutions are not affordable if they fail catastrophically.
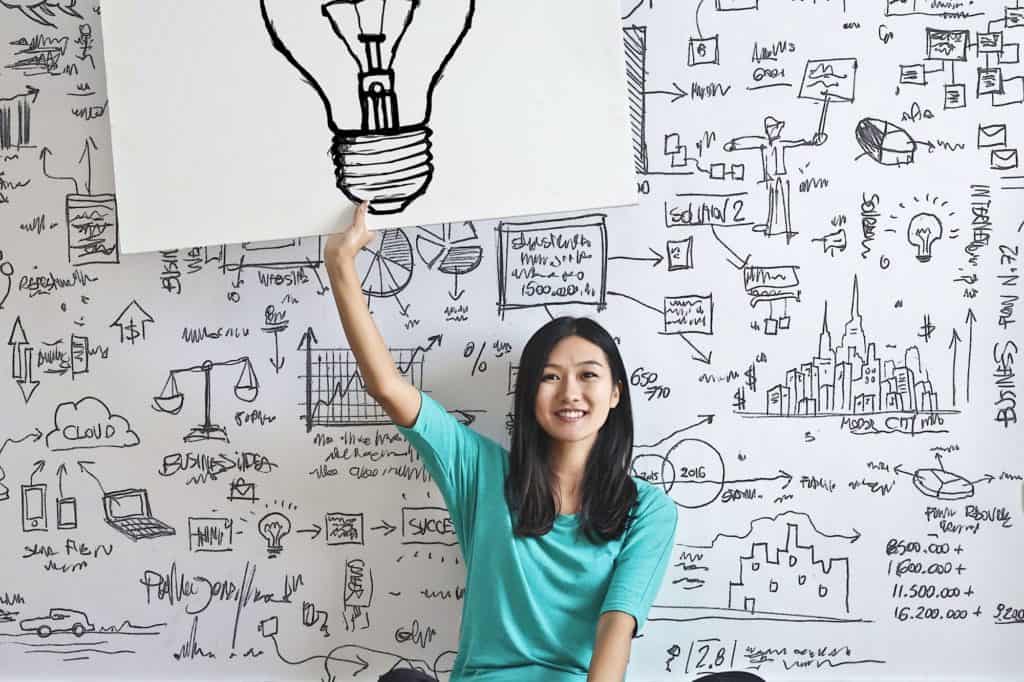
What are the essential features in selecting your thermal imager?
To maximize the value of your camera, make sure to choose a brand and model that fits your needs – from features to service and support. Your job keeps you on the move all day, taking you up ladders, into crawl- spaces, and through a rugged work environment. An excellent thermal imaging camera should offer you:
- Ruggedness – This camera is a tool, just like everything else in your toolbag. It must be rugged enough to withstand a drop from one or two meters up. It should also be easy to carry in one hand, with user-friendly buttons and menus.
- Resolution – Thermal imaging that is impossible to interpret won’t do you any good. Choose an infrared camera with enough resolution to create clear, crisp images that you can enlarge. For example, FLIR cameras offer Multi-Spectral Dynamic Imaging (MSX®), which embosses visual details onto the full-resolution thermal image. MSX® adds perspective to the scene and allows you to read text and labels.
- Reporting – Once you’ve surveyed a problem area, you must generate a report to plan the necessary repairs. FLIR pairs its cameras with FLIR Tools+, an image editing and reporting software. You can use this program to instantly generate reports with information on the problem type, location, and steps needed to resolve it. Many cameras fit these needs and are available on the market.
Which infrared camera brand should you choose?
A well-established brand should be able to offer you:
- Variety – Different users have different needs. The manufacturer must offer you a full range of thermal imaging cameras, from affordable entry models to advanced high-end models, so that you can choose the one that best fits your needs.
- Accessibility – Whatever your application, you need to be able to view and share thermal images quickly and have the software to analyze and report your findings. Choose a thermal imaging camera that works with the correct software for your application.
- Service – While most thermal imaging cameras for facilities maintenance applications are as good as maintenance-free, accidents can happen. Your camera may also need occasional recalibration. Rather than having to send your camera halfway around the world, make sure the manufacturer offers a local repair center. That way, you’ll get the camera fixed and back at work as fast as possible.
- Accessories – Ensure you have a system that can grow with your needs. The manufacturer you choose should be able to offer different types of lenses, displays, and other accessories.
- Training – There is more to the world of thermal imaging than just knowing how to handle the camera. Select a manufacturer that offers proper training and application support when needed.
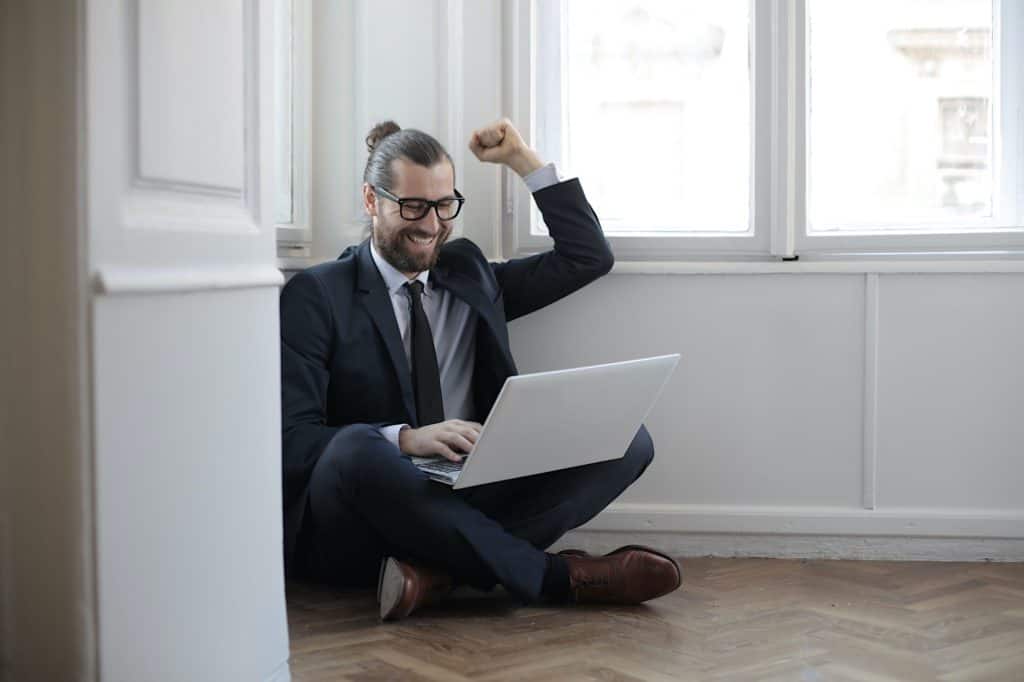
What affects your ability to measure temperatures with thermal imaging cameras accurately?
Some of the most critical factors influencing thermal measurements are:
- Thermal conductivity – Different materials conduct heat differently and have different thermal properties. For example, insulation material warms slowly, while metal objects warm up quickly.
- Emissivity – Emissivity, or the power of a surface to emit heat by radiation, is the most critical factor for correct thermal measurement.
- Reflection – Some materials are more reflective and reflect thermal radiation, just like a mirror reflects visible light.
- Indoor and outdoor temperatures – To detect missing, damaged, or inadequate insulation using thermal imaging cameras requires a noticeable difference between inside and outside temperatures – usually around 10°C.
- Building material influences – Direct sunlight affects thermal measurements, but indirect sunlight can also have long-lasting effects.
- Heating and ventilation systems – External influences such as HVAC affect indoor measurements, particularly surface temperatures.
- Influences on the inside of the building -Accessories and furniture, such as Bookshelves, cabinets, and even hanging pictures, have an insulating effect and could affect measurements.
- Reflections from the surroundings – When scanning reflective targets, you should try to minimize the reflections on the image by adjusting the camera angle you use.
- Type of materials used in the construction – Some materials, such as concrete, are “thermally slow” or change temperature very slowly.
- Methods used in constructing the building – For example, when building outer walls with an air gap between the facade and the shell, you create a temperature differential.
A Thermal imaging inspection validates various industrial processes – heat staking, hot-plate plate welding, infrared welding, laser welding, plastic joining operations, ultrasonic welding, and vibration welding, among many others. You can check the quality of your assemblies or monitor the condition of tooling using this fascinating technology.
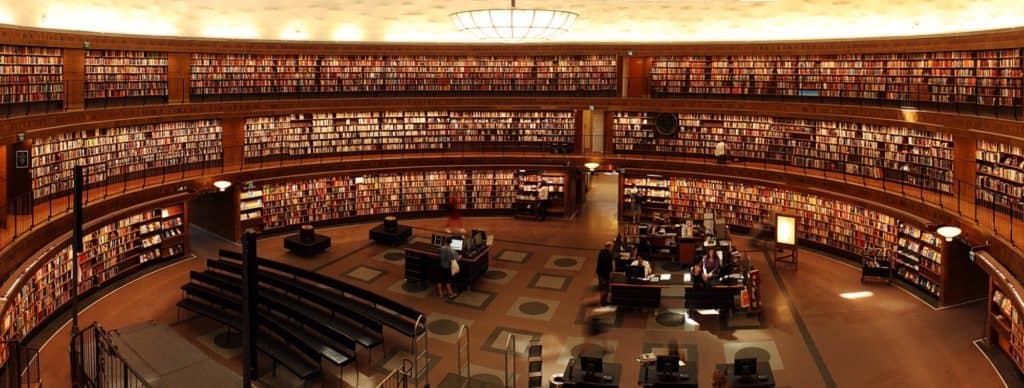
Resources And References
- Academy of Infrared Training
- Infrared Training Center
- IR Information for the Real World
- Infraspection Institute
- Reliabilityweb
- FLIR
- SUAS Toolkit
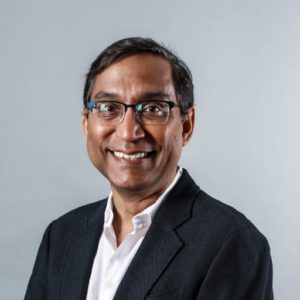
Leon Shivamber
Partner
Advisor, Entrepreneur, Strategist, & Transformation Agent
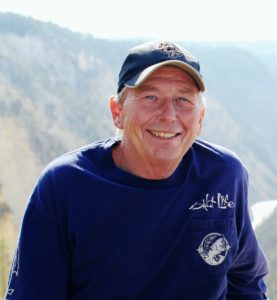
Brad Nichols
Partner
30 plus years focused on mission-critical technology and operations